1. Recover gold from gold scrap
(1) Calcination method
Applicable to copper and brass gold scrap parts, such as copper Buddha, gods, gold ware, etc., coated with sulphur (sulfur) and diluted with concentrated hydrochloric acid paste, and then placed in a fume hood After standing for 30 minutes, it was placed in a muffle furnace and calcined at a temperature of 700 to 800 ° C for 30 minutes. A layer of copper sulfide and copper is formed between the gold and the base metal, and the hot metal scrap is taken out of the furnace and placed in cold water, and the gold layer is peeled off from the copper or brass together with the scale. The gold that has not fallen off can be brushed off with a wire, filtered and dried, and the ingot is smelted.
(2) Incineration method
Suitable for scrap metal scraps of wood, paper and cloth. The paste member is placed iron pot, carefully burned ash melting gold to obtain a crude gold.
(3) Pumice method
Applicable to remove the gold from the larger gold parts. Carefully scrape the gold with a pumice block, and remove the dust and fine mud from the pumice block and the gold-plated piece with a damp sponge, wash the sponge, and the gold and pumice powder sink to the bottom of the tank, filter and dry, and cast the crude gold.
(4) etching method
Applicable to the recovery of gold from gold scraps, gold characters, signboards and other gold scraps. Wet the gold-plated article with a hot concentrated caustic soda solution every 15 minutes. When the putty and the caustic soda are saponified, the gold can be washed with a sponge or a brush. The washed gold is filtered, dried, and cast to obtain coarse gold.
(5) Electrolysis method
Applicable to all kinds of copper gold scrap pieces. The basket was charged scrap as the anode, a cathode lead plate, the electrolyte formulation, the electrolysis current density 120 ~ 180A / m 2 with concentrated sulfuric acid. The gold sinks at the bottom of the tank, and some of the gold mud adheres to the metal surface and is easily washed off. After electrolysis for a period of time, the electrolyte is diluted with water, boiled, allowed to stand for 24 h, filtered and washed with water, and the precipitate is dried and cast to obtain crude gold.
2. Recovery of gold from gold-containing dust
Such raw materials come from the ash throwing of the gold pen tip of the gold pen factory, the scrap of the gold foil factory, the dust generated by the polished open chain hammer of the jewelry factory, the abrasive of the nylon spinneret manufactured by the textile mill machinery, etc. The treatment method is:
(1) Fire smelting
The collected gold-containing dust is sieved to remove coarse sand, rubble and other impurities, and is mixed according to the ratio of dust: lead oxide: sodium carbonate: saltpetel = 100: 1.5: 30: 20, stirred evenly, placed in a crucible, and then covered with a thin boron sand, into the furnace smelting Degui lead. The ash is blown thick. When the crude gold contains platinum rhodium , it can be dissolved in aqua regia to further separate platinum and rhodium.
(2) Wet separation
The gold-plated platinum-plated ash is first dissolved in aqua regia, 铱 is insoluble in aqua regia, and filtered to obtain glutinous rice. The filtrate was treated with ammonium chloride saponin (NH 4 ) 2 PtCl 6 , and the filtered filtrate was then reduced with sulfur dioxide.
Third, recover gold from gold-containing garbage
There are many types of gold-containing garbage, and the method of collecting gold should be selected according to its type. For example, the removal of the precious metal furnace and the sweeping of the garbage can be directly returned to the lead or copper smelting workshop, such as melting in the charge, and then recovering gold from the anode mud; removing the garbage formed by the ancient buildings, the wood can be incinerated, and the smelting and ash can be crude. . The shale can be recovered and extracted by panning, re-election or cyanidation.
Fourth, recover gold from gold scrap ceramic waste
The gold may be recovered by the above-mentioned chemical method of gold plating, and the gold may be recovered by the cyanidation method or the aqua regia method. Gold is recovered from the pulverized porcelain containing 10 to 100 g/t of gold by the thiourea method, and the recovery rate is 98% to 99%.
5. Recover gold from the glass surface of the gold-plated film
Gold is recovered from the glass surface of the gold-plated film by removing the gold from the glass surface with a non-toxic acid halide solution and recovering it as gold powder. The operation steps are as follows: (1) contacting the surface of the gold-plated glass with an acidic aqueous solution of NaCl or NH 4 Cl and releasing it from the surface of the glass; (2) removing the glass from the solution to precipitate the gold powder at the bottom of the solution; (3) Filter out the gold powder. Drying and smelting; (4) The solution of the acid halide is preferably an aqueous solution of 1% to 6% of NaCl and NH 4 Cl or 1% to 5% of H 2 SO 4 .
This method is suitable for recovering gold from scrapped gold-plated architectural glass, and the method has the advantage of being non-toxic.
6. Recover gold from gold brushes and gold water bottles
In the daily-use ceramic gold-plating process, the brush used for gold extraction, the residual glass bottle used for the gold water, saturate and saturate the gold water slurry condensation. Such materials can be recovered by calcination or leaching. The calcination temperature at the time of processing the gold brush was controlled at 800 ° C, and the temperature of the calcined gold water bottle was 400 ° C. Leaching the solvent may be aqua regia, after the leaching solution was replaced with zinc nitrate powder catch reduction. The grade of gold powder produced can reach 95%.
7. Recovery of gold from jewelry waste
The process of regenerating from jewelry waste has been studied, and this issue is important because it contains a lot of valuable gold in the waste. However, it is difficult to solve this problem because the physical form and chemical composition of the waste vary greatly. According to the literature, the solvent extraction process seems to be very promising for solving this problem. Based on a large number of experiments, AGChmielewski designed a process flow as shown in Figure 1:
Figure 1 Hydrometallurgical process flow chart for gold recovery
(1) Low temperature carbonization and roasting of waste;
(2) performing the first step of leaching with a nitric acid solution to separate silver and other metals;
(3) performing the second step of leaching with nitric acid-hydrochloric acid (Aqua regia);
(4) extracting gold with a selective solvent of diethyl malonate;
(5) Separating metal gold from the organic phase by a reduction method.
The thermal degradation process was studied by differential thermal analysis and other methods. The effects of temperature, batch mixing and heating time were investigated. The optimum conditions are determined: the waste is added to a cold burning furnace, and the temperature is continuously raised to 750 ° C within 4 to 5 hours, and then the waste is digested at 750 to 850 ° C for 3 hours, and stirred periodically for 3 to 4 times. The content of gold in the slag is 3% to 10%. The effects of nitric acid concentration, stirring time, temperature and liquid-solid ratio on the first leaching were investigated. As a result, the following process parameters were selected: a concentration of nitric acid of about 8 mol/L (1:1 dilution of concentrated nitric acid), a temperature of 40 to 50 ° C, a stirring time of about 7 h, and a liquid: solid = 5:1.
In the second step, aqua regia was used to study the effects of temperature and agitation time. The best results were obtained at 40-60 ° C for 7 h. In the solid residue, the content of gold does not exceed 0.03% to 0.08%. In addition to gold, the resulting solution contains other elements: B, Si, P, Fe, Mn, Pb, Bi, Sn, Ti, Ag, Ca, Cu, Na, and Zn.
For the purification of gold, a liquid-liquid extraction process was selected. The extractive agents were studied: ethanol, methyl-isobutyl ketone, di-n-butyl ketone, diethyl malonate, dibutyl ether, ethylene glycol, n-pentyl ether, 2.2 dichloroethyl ether, TBP and Several natural petroleum fractions. The main characteristics considered are: selectivity, potential loading for gold, resistance to contact with water, organic phase, separation of aqueous phase and extractant price. After the gold is dissolved in the hydrochloric acid hydrochloric acid, the correct extraction parameters must be determined, such as the appropriate aqueous phase acidity (aqua regia dilution), the high extraction coefficient value, and the effect of the gold concentration in the feed liquid (extraction isotherm). ). When these parameters are transformed using conventional analytical methods, the extraction is determined by using a radioactive tracer element 198 Au with a half-life of 2.5 d and a decay energy of γ = 411 kev, since it is subject to changes in extraction efficiency that are both costly and time consuming. coefficient. The aqueous solution containing gold king was traced with a radio tracer. Such radiotracers are obtained by exposing high purity metal gold to a nuclear reactor for radiation and then dissolving it in a small amount of aqua regia. The extraction test was carried out in a separatory funnel. After the two-phase separation, the multiple organic phase and the aqueous phase were separately sampled, and the radiation intensity was measured by a semiconductor detector Ge (Li) coupled to a multi-channel pulse amplification analyzer, and then the extraction coefficient was calculated (taken by the ratio of the two-phase radiation intensity) The ratio of gold to gold) and the extraction rate.
Based on the results obtained, diethyl malonate was selected as the best extractant for industrial application research. The extractant exhibits a high extraction coefficient (only one extraction is sufficient to achieve quantitative separation of gold) and the highest gold saturation capacity (140 g/L) under good conditions, as well as good selectivity. These suitable conditions are: the contact time is not less than 10 to 10 minutes, the aqueous solution of the king is diluted to at least 1:1, the phase volume ratio is O/A = 1/1, and the phase separation time is about 30 minutes.
The structure of the strong complex of gold and extractant was investigated by IR, UV, NMR and mass spectrometry. It has been determined that its structural formula is CH 2 (COOC 2 H 5 ) 2 Au(H 2 O) 4 Cl 3 , which is independent of the gold concentration in the extractant. The malonate is symmetrically complexed with two oxygen atoms which may be derived from the ether group.
In order to purify the gold, the organic phase extract was washed by adding 0.01 mol/L of HNO 3 and stirring for 15 min at a ratio of 1:1, and almost all impurities were quantitatively removed.
Two methods for the reduction of gold from extracts have been developed and patented. First, at a temperature of 80 to 90 ° C, sulfuric acid, 30% H 2 O 2 and oxalic acid are successively added to degrade the extract. Second, the gold is reduced by using saturated ferric sulfate as a reducing agent at a temperature of 80 ° C without degrading the extract. The reducing agent can be used multiple times. In both methods, the metal gold can be precipitated within a few minutes, the purity of the obtained gold powder is 99.99%, and the total gold recovery is about 97%. Assume that the repayment period is 10 years. The economic benefit coefficient of the technology calculated based on the ratio of gold recovery to production and investment costs is 2.7.
The special units in the gold recovery methods mentioned above have been used to recover gold from various wastes produced by the electronics industry.
PIV Laser
Particle Image Velocimetry (PIV) achieved significant development compared with traditional flowing display technology by using a transient, multi-point, non-contact hydrodynamic speed method. PIV overcome the single point measurement limitations of traditional means for that PIV can record a great deal of velocity distribution of different space at the same transient state, also provide customers affluent spatial structure and flowing characteristics about the flow field. PIV can be widely used in the wind tunnel flow field measurements, turbulent flow field measurements, particle flow studies, environmental studies, biomedical research and other fields.
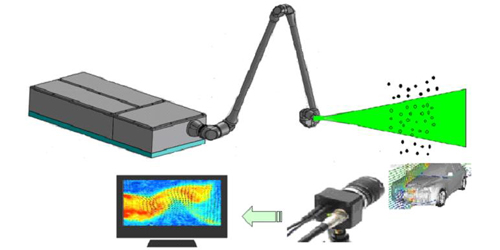
â– CNI
self-made high performance Laser source
â– All accessories for PIV test system
â– Easy to Install, uninstall and maintain
â– Adapt to harsh PIV environment
â– Provide customized solutions
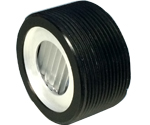
|
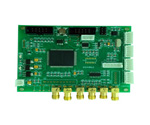
|
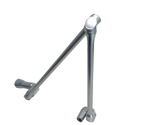
|

|
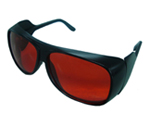
|
Laser Light Sheet
|
Synchronizing System
|
Articulated Arm
|
Remote Control System
|
Laser Goggles
|
The experiment phenomena of CNI laser for PIV from customers
|
Laser for Particle Image Velocimetry,Particle Image Velocimetry,Particle Image Velocimetry Measurement Systems,Particle Image Velocimetry Lasers
Changchun New Industries Optoelectronics Technology Co., Ltd. , https://www.opticsqm.com